In the world of Liquefied Natural Gas (LNG), navigating subzero conditions is not just a challenge—it’s a way of life. For operations that depend on precision and reliability, having equipment that can withstand these harsh environments is crucial. Enter the VT1000, a game-changer designed to excel in subzero LNG environments. This blog post will explore the intricacies of the VT1000, its unique features, and its real-world applications in overcoming subzero challenges in LNG operations.
The Role of VT1000 in Subzero LNG Environments
The VT1000 is not merely another piece of equipment; it is a technological marvel tailored to meet the unique demands of subzero LNG environments. LNG operations require machinery that can operate flawlessly in temperatures that would render most standard equipment ineffective. The VT1000 steps up to the plate with unparalleled reliability.
The primary role of the VT1000 in subzero LNG environments is to ensure smooth and efficient operations despite plummeting temperatures. This equipment has been specifically engineered to handle the unique challenges posed by such harsh conditions. It provides the operational stability and robustness that LNG projects in extreme cold climates desperately need.
What sets the VT1000 apart is its adaptability. While other machines might freeze up or fail, the VT1000 continues to function optimally, ensuring that LNG operations can proceed without costly interruptions. Its role in these environments is indispensable, making it a preferred choice among industry professionals.
Understanding the Challenges of Operating in Subzero Conditions
Subzero conditions present a host of challenges that can severely impact LNG operations. One of the most significant obstacles is the risk of equipment freezing. When temperatures drop below zero, standard machinery often becomes brittle and prone to failure, leading to operational downtime and increased maintenance costs.
Another challenge is reduced efficiency. Equipment that is not designed for subzero environments tends to perform at a lower efficiency rate, which can hinder overall productivity. This reduction in efficiency is not just a minor inconvenience; it can have a substantial negative impact on the entire LNG supply chain.
Additionally, there is the issue of safety. Operating in subzero conditions significantly raises the risk of accidents. Icy surfaces, frozen equipment, and decreased human dexterity due to cold can lead to hazardous situations. Ensuring the safety of personnel and machinery is paramount, and this is where specialized equipment like the VT1000 proves invaluable.
The Unique Features of VT1000 for LNG Environments
The VT1000 boasts several unique features that make it ideally suited for subzero LNG environments. First and foremost is its rugged construction. Built with materials that can withstand extreme cold, the VT1000 remains operational even when temperatures plummet. This durability is a key factor in its widespread adoption in the LNG sector.
Another standout feature is its advanced thermal management system. The VT1000 is equipped with innovative thermal regulation technology that prevents freezing and ensures consistent performance. This system maintains optimal operating temperatures for the machine, thereby enhancing its reliability.
Furthermore, the VT1000 offers superior energy efficiency. Its design includes energy-saving mechanisms that reduce power consumption without compromising performance. For LNG operations, this means lower operational costs and a reduced environmental footprint.
Real-World Applications and Success Stories
The VT1000 has proven its worth in various real-world applications within subzero LNG environments. One notable success story comes from an LNG facility in Northern Canada, where the VT1000 played a pivotal role in maintaining seamless operations throughout the harsh winter months. Despite temperatures dipping to -40°F, the VT1000 demonstrated remarkable resilience, ensuring uninterrupted gas extraction and processing.
Another example is from a Siberian LNG project where the VT1000 was instrumental in overcoming the challenges posed by the region’s frigid climate. The machinery’s ability to function flawlessly in such extreme conditions reduced downtime and enhanced overall project efficiency, showcasing its robustness and reliability.
These success stories underscore the VT1000’s capability to thrive in some of the world’s most challenging LNG environments. They highlight how the equipment’s advanced features translate into tangible benefits for operators, making it a trusted solution for subzero LNG operations.
Technical Specifications and Advancements
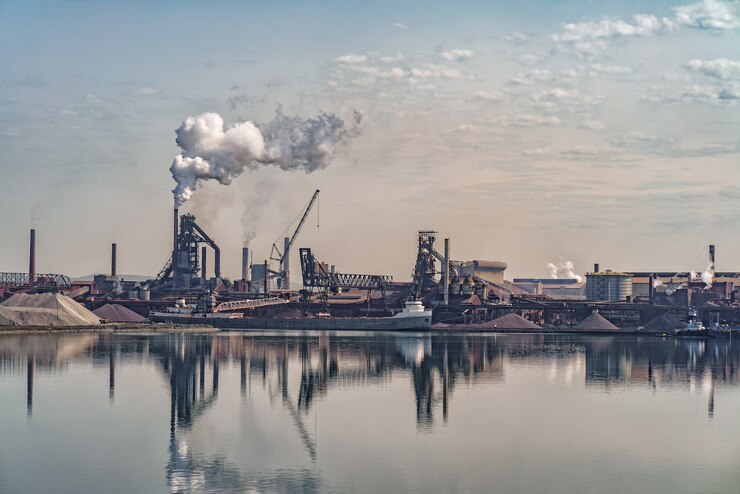
The technical specifications of the VT1000 are a testament to its engineering excellence. It features a high-torque motor designed for low-temperature operations, ensuring consistent performance without the risk of freezing. The motor is complemented by an advanced lubrication system that remains effective even in extreme cold, protecting the internal components from wear and tear.
Additionally, the VT1000 incorporates state-of-the-art sensors and control systems that monitor and adjust its performance in real-time. These sensors provide valuable data on operating conditions, allowing operators to make informed decisions and optimize efficiency. The control systems also include fail-safes that automatically shut down the machine in case of anomalies, ensuring safety and preventing damage.
One of the latest advancements in the VT1000 is its integration with IoT technology. This connectivity allows for remote monitoring and diagnostics, enabling operators to identify and address potential issues before they escalate. The combination of IoT and advanced control systems makes the VT1000 a highly intelligent and responsive piece of equipment.
Future Developments and Impact
The future of the VT1000 in subzero LNG environments looks promising, with ongoing developments aimed at enhancing its capabilities. Researchers and engineers are continually working on improving the machine’s energy efficiency, durability, and smart features. These advancements are expected to further solidify the VT1000’s position as the go-to solution for subzero LNG operations.
One area of focus is the development of even more robust materials that can withstand the harshest conditions without compromising performance. Innovations in material science are likely to yield new components that enhance the VT1000’s durability and longevity.
Another exciting development is the potential integration of AI-driven predictive maintenance. By leveraging AI algorithms, the VT1000 could predict and preemptively address maintenance needs, minimizing downtime and maximizing operational efficiency. This advancement would represent a significant leap forward in the realm of smart machinery for LNG operations.
Conclusion
The VT1000 stands as a beacon of innovation and reliability in the challenging world of subzero LNG environments. Its unique features, coupled with real-world success stories, underscore its indispensability for operators facing the harshest conditions. With ongoing advancements and a promising future, the VT1000 is poised to continue making a significant impact on the LNG industry.